Closing the loop for all industrial liquid cooling solutions.
PC 2500, CCE, EB series – air and water cooled ready-to-connect chillers. Due to the new EU regulation, all of our chillers are already converted to common, lower impact refrigerants.
The 100 % system solution for all sectors of industry.
Moreover, chillers can be combined with air/water heat exchangers in a maintenance-free solution and offer decisive advantages in applications where the ambient conditions are too aggressive for conventional cooling units or a very high IP is required. The areas of application for chillers range from machine tools, lasers, plastic processing and alternative energy to food, drinks and pharmaceutical industries.
Our staff are always on hand to discuss the application, to make sure that a proper selection is made and to provide technical assistance – see service. Especially for chillers, the professional commissioning by trained service technicians from Pfannenberg is crucial for a long term and fail-safe cooling.
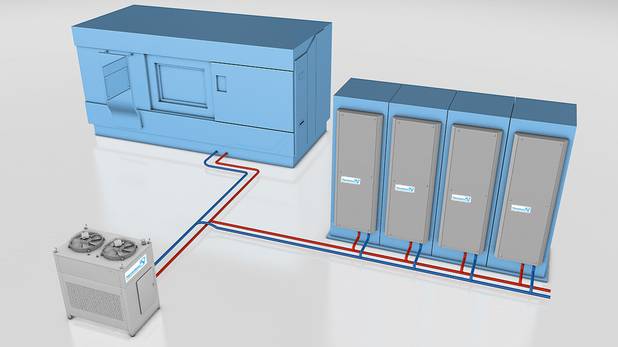
It’s about reliability, efficiency and long service life.
Pfannenberg’s chillers guarantee a central and cost-effective solution and perfectly answer industry's need for precise temperature control and absolute reliability, 24 hours a day, 365 days a year. Design is compact, maintenance friendly and they easily match global requirements due to the flexibility in terms of certifications such as UL. More than 20 year experience in the field and the use of high quality components ensure optimum long-term stability and high MTBF (Mean Time Between Failures) reliability rates.